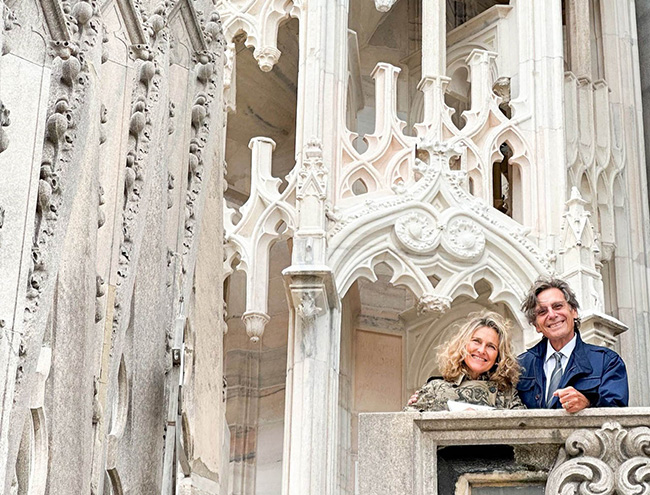
10 mars 2020
Machining Navi
La vibration est assez courante dans le domaine des machines-outils CNC, le Machining Navi d’Okuma a été développé pour traiter les paramètres de coupe optimaux avec lesquels la machine peut annuler cette vibration, en économisant ainsi du temps à l’opérateur et maximisant la productivité. Okuma a développé le Machining Navi, une fonctionnalité optionnelle du contrôle OSP qui utilise des capteurs ou un microphone pour surveiller les vibrations. Si une vibration est détectée, la fonction propose de modifier la vitesse de la broche (Machining Navi L-g et Machining Navi M-g) ou de modifier automatiquement la vitesse de la broche et la progression du travail (Machining Navi M-i NO retrofit). Il permet aussi l’emploi d’outils standard et évite dans certains cas des coûts supplémentaires et une perte de temps pour le client pour l’achat d’outils spéciaux.
Concept Thermo-Friendly
On ne combat pas la déformation thermique, on travaille avec, c’est le concept d’Okuma. Thermo-Friendly Concept permet d’améliorer la précision, d’économiser du temps et de réduire l’incidence des déchets en contrôlant ce qui semble être incontrôlable.
Le Thermo-Friendly Concept est né au moment de la conception symétrique de la structure machine pour la gestion du problème de la dilatation thermique et faire face à cet élément qui ne peut être éliminé. L’union de l’hardware et du logiciel Okuma garantit une compensation thermique extrêmement précise en gérant la dilatation à tout moment de la journée à partir de 0.1 micron, garantit aussi une stabilité dimensionnelle sans précédent pour toutes les opérations dans des lieux de travail non climatisés mais avec des variations de température de 8° sur 24 heures, et évite de perdre du temps et donc de l’argent dans le réglage quotidien de la machine.
Le Thermo-Friendly d’Okuma est standard sur tous les modèles.
Collision Avoidance System (Système anticollision)
Vu que les machines deviennent de plus en plus complexes, impliquant notamment des axes rotatifs supplémentaires, l’automation et le changement incessant de la configuration de la machine, il y a plus de place pour l’erreur humaine.
Notre système d’anticollision CAS (standard sur toute la série MULTUS) intègre la modélisation 3D de nos machines dans les moindres détails et donne la possibilité aux clients d’introduire facilement des dessins d’équipements et d’outils dans le contrôle OSP pour créer à tous les effets une machine virtuelle. La commande numérique OSP calcule virtuellement tout le processus et, en cas de collision imminente, arrête la machine en évitant le risque de panne et de frais de la part du service.
Le CAS génère la forme réelle et exacte de la pièce pendant le cycle, en mettant continuellement à jour le nouveau produit brut pour avoir toujours le processus sous contrôle et analyser qu’il n’y ait pas d’interférences ni de collision.
Il maximise les temps de réglage de la machine et permet aux opérateurs de se concentrer sur l’usinage.
Il protège la machine des erreurs de l’opérateur même en mode manuel, jog, rapide et MDI.
5-axis-auto-tuning
Lors de l’usinage avec une machine-outil CNC à 5 axes, il est courant que des erreurs géométriques influencent la qualité et la précision de la pièce. De l’installation à l’utilisation de la machine-outil au fil du temps, il peut se rendre nécessaire de vérifier la cinématique, les causes les plus courantes sont le dénivelé de la machine par rapport au sol ou un autre exemple peut être des petites collisions dues aux erreurs d’utilisation à causer ces erreurs géométriques. Pour conserver un usinage à 5 axes de haut niveau, il faut effectuer un réglage très précis pour compenser les erreurs géométriques éventuelles.
La fonction 5 axis auto turning permet à la machine de requalifier rapidement et avec précision la géométrie en compensant jusqu’à onze erreurs géométriques.
La requalification peut être rapidement effectuée par l’opérateur sans un haut niveau de compétence dans l’utilisation de la machine, en évitant la longue intervention d’un technicien.
Il existe 11 types possibles d’erreurs géométriques sur les machines à 5 axes, le déplacement de la position du centre de rotation des axes rotatifs, l’inclinaison de l’axe rotatif par rapport à l’axe orthogonal, la déformation thermique et les variations dans le temps sur l’emplacement de la machine.
Servonavi
Le SERVONAVI d’Okuma est une technologie de haute précision qui améliore la durée des cycles et la précision pendant l’usinage des pièces. Cette technologie est STANDARD sur tous les centres d’usinage Okuma à double colonne, verticaux et horizontaux (sauf Genos-M). Dans les centres d’usinage précédents, il n’y avait pas la possibilité de varier l’accélération réelle avec différentes charges sur la table (pièce, équipement) c’est aujourd’hui possible. La fonction de réglage automatique du poids du SERVONAVI calcule automatiquement les charges pour ajuster la meilleure vitesse d’accélération et décélération pour obtenir des temps de cycles plus rapides et pour utiliser au mieux l’électronique et la mécanique.
Il est aussi possible de régler automatiquement l’inversion des axes pour obtenir au fil du temps une interpolation toujours très précise.
Les vibrations causées par le glissement linéaire des axes peuvent être ajustées automatiquement lorsque les conditions de la machine varient au cours du temps.
Le logiciel SERVONAVI est également présent sur les tours pour gérer automatiquement l’inertie sur la broche et garantir des superbes finitions sur les surfaces tournées.